Get consistent results with expert plastic extrusion techniques
Get consistent results with expert plastic extrusion techniques
Blog Article
Checking Out the Different Methods and Technologies Behind Plastic Extrusion
The world of plastic extrusion is a blend of modern technology, development, and accuracy, pivotal to various industries worldwide. Advanced machinery, digital controls, and an array of materials merge in this complex process, generating top quality, sturdy products.
Comprehending the Essentials of Plastic Extrusion
The process of plastic extrusion, typically hailed as a cornerstone in the world of production, forms the bedrock of this discussion. Fundamentally, plastic extrusion is a high-volume production procedure in which raw plastic material is melted and developed right into a continual account. It's a method commonly utilized for producing things with a consistent cross-sectional profile, such as pipes, window frameworks, and weather condition removing. The procedure starts with feeding plastic products, usually in the form of pellets, into a heated barrel. There, it is blended and heated till it ends up being molten. The liquified plastic is after that required with a die, forming it right into the preferred type as it solidifies and cools down.
The Duty of Various Materials in Plastic Extrusion
While plastic extrusion is a frequently utilized method in manufacturing, the materials made use of in this procedure substantially affect its final output. Various kinds of plastics, such as polyethylene, abdominal, and pvc, each offer special homes throughout product. Polyethylene, known for its durability and adaptability, is typically used in product packaging, while PVC, renowned for its strength and resistance to ecological elements, is made use of in building. ABS, on the various other hand, integrates the very best qualities of both, resulting in high-impact resistance and sturdiness. The choice of product not only influences the product's physical buildings yet likewise influences the extrusion speed and temperature level. For that reason, suppliers should meticulously consider the buildings of the material to enhance the extrusion procedure.
Strategies Made Use Of in the Plastic Extrusion Refine
The plastic extrusion procedure entails numerous strategies that are critical to its operation and performance (plastic extrusion). The conversation will certainly start with a streamlined description of the essentials of plastic extrusion. This will certainly be followed by a breakdown of the process carefully and an exploration of approaches to boost the performance of the extrusion strategy
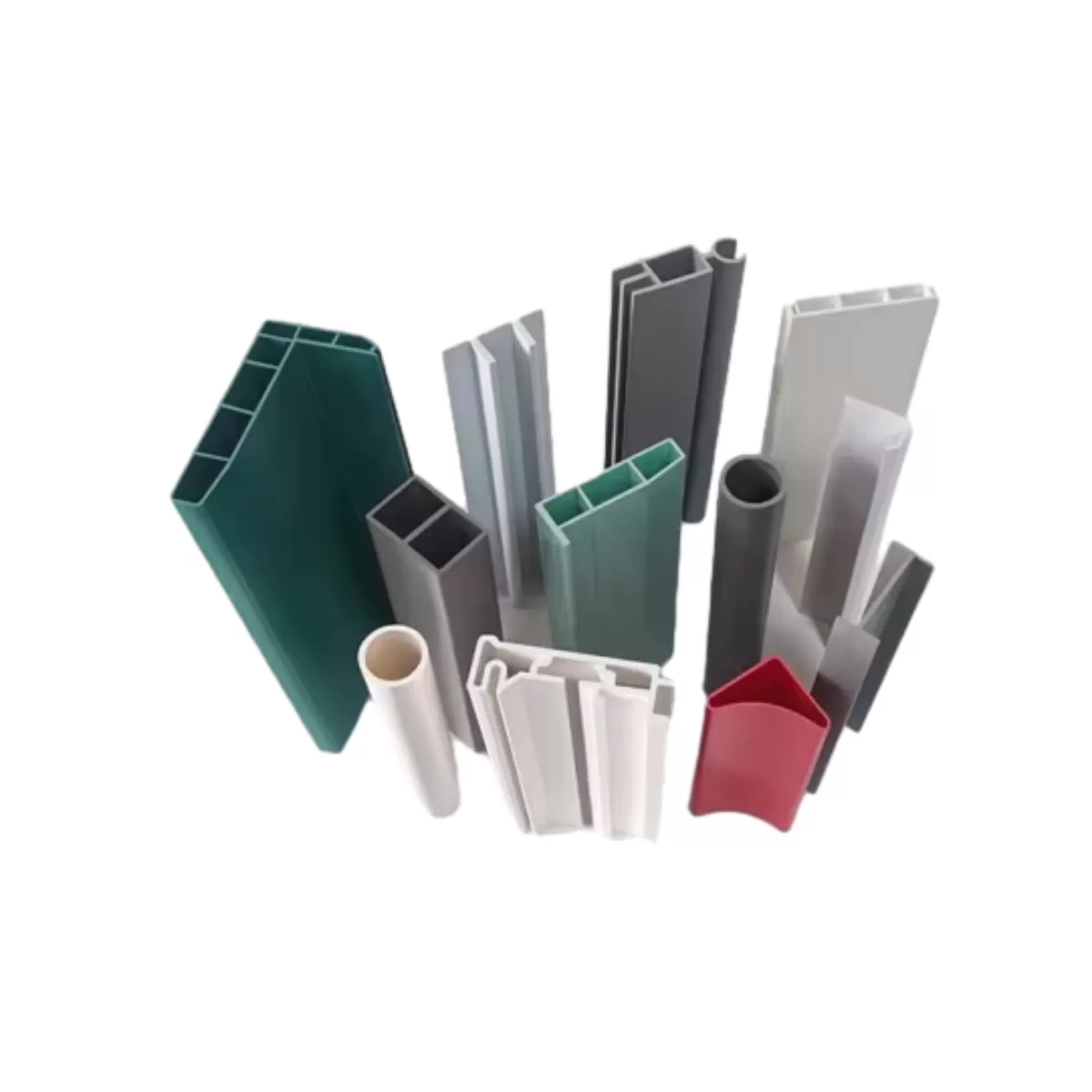
Understanding Plastic Extrusion Basics
In the realm of production, plastic extrusion stands as an essential process, important in the production of a plethora of day-to-day products. At its core, plastic extrusion involves changing raw plastic material into a continual profiled shape. This is achieved by thawing the plastic, typically in the form of granules or pellets, and requiring it through a designed die. The resulting product is a lengthy plastic piece, such as a pipe, cord, or panel coating, that preserves the shape of the die. This cost-effective technique is highly functional, able to create intricate shapes and suit a wide range of plastic materials. Basic understanding of these fundamentals permits for additional expedition of the much more detailed aspects of plastic extrusion.
Comprehensive Extrusion Refine Breakdown
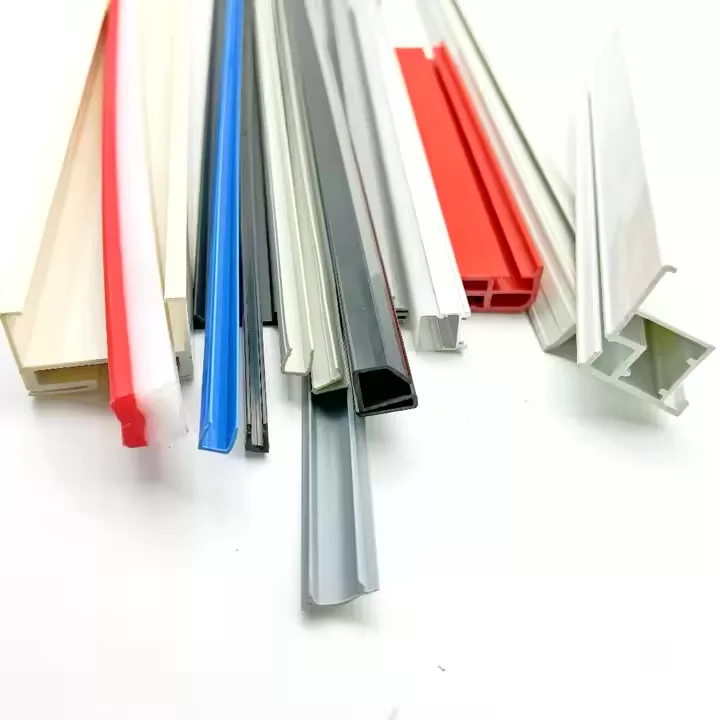
Improving Extrusion Method Efficiency
Efficiency gains in the plastic extrusion procedure can considerably impact both the top quality of the final item and the general productivity of the operation. Continual optimization of the extrusion strategy is important to preserving an one-upmanship. Techniques that improve efficiency commonly involve specific control of temperature and stress throughout the process. Modern modern technologies, such as electronic systems and sensing units, have contributed in achieving this control. In addition, using high-quality resources can lower waste and improve result top quality. Routine maintenance of extrusion equipment can likewise minimize downtimes, therefore boosting productivity. Adopting lean manufacturing principles can aid remove unnecessary steps in the process, advertising performance gains.
Just How Technology Is Changing the Face of Plastic Extrusion
The advent of new technology has actually substantially changed the landscape of plastic extrusion. It has actually caused the advancement of sophisticated extrusion machinery, Full Report which has enhanced the efficiency and quality of the plastic extrusion procedure. Furthermore, innovations in the extrusion procedure have actually likewise been driven by technological developments, supplying improved capabilities and versatility.
Advanced Extrusion Equipment
Reinventing the realm of plastic extrusion, advanced equipment imbued with advanced technology is introducing a new era of performance and precision. These machines, outfitted with ingenious features like automatic temperature control systems, ensure optimum conditions for plastic handling, thus minimizing waste and boosting product top quality. High-speed extruders, for example, intensify outcome prices, while twin-screw extruders use superior blending abilities, crucial for producing intricate plastic blends. Additionally, electronic control systems supply unprecedented precision in operations, decreasing human error. Moreover, these makers are created for long life, decreasing downtime and upkeep expenses. While these advancements are already impressive, the continuous development of modern technology promises even better leaps forward in the area of plastic extrusion equipment.
Technologies in Extrusion Procedures
Harnessing the power of modern technology, plastic extrusion procedures are undertaking a transformative transformation. Innovations such as digital mathematical control (CNC) systems currently enable even more accuracy and consistency in the production of extruded plastic. Automation even more enhances efficiency, reducing human mistake and labor prices. The assimilation of expert system (AI) and maker discovering (ML) algorithms is transforming quality control, forecasting inconsistencies, and boosting the general performance of extrusion procedures. With the arrival of 3D printing, the plastic extrusion landscape is additionally broadening into brand-new worlds of possibility. These technical innovations are not just enhancing the quality of extruded plastic products however likewise pushing the industry in the direction of a much more sustainable, efficient, and innovative future.
Real-World Applications of Plastic Extrusion
Plastic extrusion, a effective and versatile procedure, discovers use in numerous real-world applications. It's predominantly utilized in the production sector, where it's made use of to create a myriad of products such as pipelines, tubings, window structures, weather stripping, and secure fencing. The automotive market additionally look at this now harnesses this innovation to generate parts like plastic and trim sheeting. Moreover, the clinical area counts on extrusion for the construction of catheters, IV tubes, and other medical gadgets. Even in food production, extrusion contributes in creating items like pasta or cereal. The strength and versatility of plastic extrusion, combined with its cost-effectiveness, make it an essential process across different sectors, underlining its widespread useful applications.
The Future of Plastic Extrusion: Forecasts and Patterns
As we look to the horizon, it comes to be clear that plastic extrusion is poised for considerable advancements and improvement. Eco-friendly options to traditional plastic, such as bioplastics, are likewise expected to get traction. These patterns show a dynamic, progressing future for plastic extrusion, driven by technical innovation and a dedication to sustainability.

Final thought
To conclude, plastic extrusion is a news complex process that uses innovative modern technology and varied materials to produce diverse items. Technical innovations, such as computerized controls, enhance the production process and make sure regular outcomes. The market's emphasis on sustainability and smart equipment recommends an encouraging future. As plastic production remains to advance, it remains a crucial part of numerous markets worldwide.
In essence, plastic extrusion is a high-volume production process in which raw plastic material is melted and created right into a continuous profile.While plastic extrusion is a generally utilized strategy in production, the materials used in this process greatly affect its final outcome. At its core, plastic extrusion involves changing raw plastic product right into a constant profiled shape. It has actually led to the growth of innovative extrusion equipment, which has actually enhanced the efficiency and top quality of the plastic extrusion process.In conclusion, plastic extrusion is a complicated process that utilizes innovative innovation and varied products to create varied products.
Report this page